Çağatay Pancaroğlu was born in İstanbul in 1972. He concluded
his primary and elementary education in İstanbul. After graduating
from Fenerbahçe highschool, he went to Eastern Mediterranean
University, Economics Department in 1992. As his scholarship
ended during his second year, Pancaroğlu was transferred to
Eskişehir Anadolu University. Çağatay Pancaroğlu started his
professional career at Eskişehir Arçelik's Human Resources
Department, right after his graduation in 1997. Apart from
many projects around the field of human resources, Çağatay
Pancaroğlu took part in 6 Sigma Project Leadership and TPM
Training Piller Leader duties. In 2001, he concluded master's
degree program for Economy Politics in Eshişehir Anadolu University.
In 2006 he started to work at CSA Holding as the Human Resoruces
Director. In January 2008, the responsibilities of two companies
within the body of Holding, Dentaş Ambalaj and Kağıt San.
A.Ş. were added under his title. Çağatay Pancaroğlu is married
and a father of two.
Awareness for Regeneration
The subject of our study: Allowing our employees to break
their shell in terms of technical and behavioral perspectives
and renewing their way of thinking.
Many processes are embraced as the right ones by our companies
and thanks to our habits, this structure is being brought
to present. With our work, we wanted to change and renew the
behavioral and technical competencies of our employees. For
making this happen we benefited the tools of quality and behavior.
But most important of all, both we and our employees shared
the same faith. We both wanted change and regeneration.
The biggest support came from our general manager and thanks
to the termless support from the top management, we have achieved
this regeneration.
First step was reviewing the selection and placement phase.
We have interviewed 40 people and got 1 person hired. We took
the orientation phase of sales team and made revisions. We
wanted to bring a new approach to the classical process. After
providing technical information about products and other processes,
our employees worked in production with each machine for 2
weeks.
What we aimed for blue-collar employees was that they could
know and understand the machines batter and retain the sufficient
skills to soothe the maintenance process. We provided basic
electrics, basic oiling, pneumatic, hydraulic, 5S and Kaizen
trainings. From the very beginning, we have picked pilot workbenches
and monitored the whole process step by step.
With trainings designed to enable sales team to break their
shell and improve their behavioral skills including;
Knowing Yourself and Creating Awareness
Balance of Business Life
Sense of Responsibility
Harmony between Mind and Body
Empathy
we allowed them to retain different point of views.
|
 |
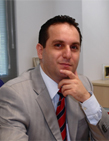 |